Classification of Stainless Steel Pipes by Manufacturing Process
Stainless steel pipes are primarily categorized into seamless and welded types, with different manufacturing processes determining their pressure resistance and application scenarios.
Manufacturing Process | Characteristics | Applications |
Seamless Stainless Steel Pipe | Produced by piercing a solid stainless steel billet, followed by hot rolling, cold rolling, or cold drawing. Offers uniform structure and high pressure resistance. | Pressure vessels, boilers, chemical pipelines |
Welded Stainless Steel Pipe | Formed by rolling stainless steel plates or strips and welding the seam. More cost-effective, suitable for fluid transportation and structural support. | Fluid transport, decorative applications, general piping connections |
The choice between seamless and welded pipes depends on specific usage requirements, from high-pressure, wear-resistant environments to standard structural support.
Classification of Stainless Steel Pipes by Material and Application
By Material
The material composition of stainless steel pipes determines their performance in various environments. Common material types include:
Material Type | Representative Grades | Key Characteristics | Application Fields |
Austenitic Stainless Steel | 304, 316L | Excellent corrosion resistance, suitable for high-sanitation environments | Food processing, pharmaceuticals, chemical industry |
Duplex Stainless Steel | 2205, 2507 | Combines advantages of austenitic and ferritic stainless steel, offering superior overall performance | Marine industry, oil and gas, heavy industry |
Ferritic Stainless Steel | 430 | Good stress corrosion resistance, cost-effective | Architectural decoration, home appliances |
Martensitic Stainless Steel
| 410, 420 | High hardness, excellent impact resistance | Machinery manufacturing, cutting tools, mold |
By Application
Stainless steel pipes serve various industrial and commercial purposes, including:
Industrial Pipes: Used in petroleum, natural gas, and chemical industries, requiring resistance to high temperatures, high pressures, and corrosive environments.
Fluid Transport Pipes: Common in food and pharmaceutical industries, ensuring hygienic and safe media transportation.
Decorative Pipes: Employed in architectural design, railings, and furniture, offering both aesthetic and functional benefits.
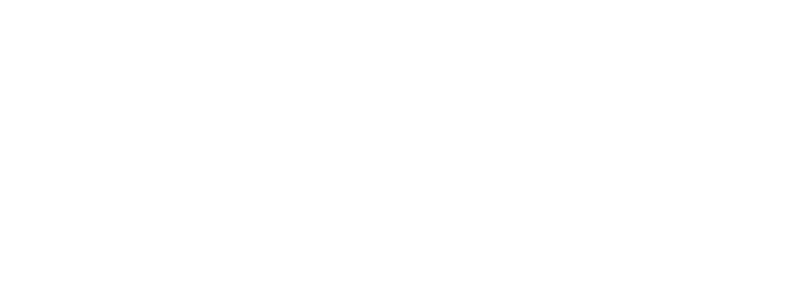
Core Advantages of Stainless Steel Pipes
Stainless steel pipes are widely chosen for their durability, strength, and resistance to environmental factors. The table below summarizes key advantages and their technical implications:
Advantage | Description | Practical Benefits |
Corrosion Resistance | Withstands acids, alkalis, and salts, ensuring long-term durability | Extends equipment lifespan, reduces maintenance costs |
High Strength | Capable of bearing high mechanical loads and withstanding extreme conditions | Suitable for heavy-duty applications and high-pressure systems |
Aesthetic & Durable | Bright surface finish, customizable with polishing or brushing treatments | Enhances architectural appeal while maintaining structural integrity |
Eco-friendly & Safe | Meets hygiene standards for food and pharmaceutical industries | Non-toxic, ensuring health and safety compliance |
Choosing the appropriate stainless steel pipe for an engineering project involves matching the material and manufacturing process with the intended application. Environmental conditions and the nature of the transported medium should also be considered. For instance, food processing plants require sanitary-grade stainless steel pipes, while chemical plants prioritize corrosion and heat resistance. Before procurement, it is essential to review product specifications, supplier credibility, and compliance with industry standards such as ASTM and GB/T.